
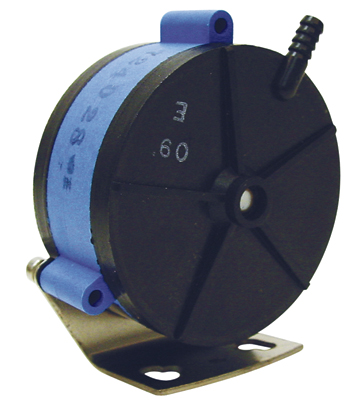
The proposed HC system was supported by a custom-designed delivery system for one of the distribution centers.Ĭontinuing on the holistic sales path, the team inquired about the time and resources required for storage and handling of the current protective packaging products. Differential pressure sensing techniques can be used to produce angle of attack and angle of sideslip indications.IPS Packaging reviewed the customer’s entire packing process instead of limiting the audit to just the packing materials. Depending on the design, such air data probes may be referred to as 5-hole or 7-hole air data probes. Some pitot-static systems incorporate single probes that contain multiple pressure-transmitting ports that allow for the sensing of air pressure, angle of attack, and angle of sideslip data. When the aircraft climbs, static pressure will decrease. It incorporates a second coaxial tube (or tubes) with pressure sampling holes on the sides of the probe, outside the direct airflow, to measure the static pressure. A pitot-static tube effectively integrates the static ports into the pitot probe. An alternative static port may be located inside the cabin of the aircraft as a backup for when the external static port(s) are blocked. With this positioning, an average pressure can be taken, which allows for more accurate readings in specific flight situations.
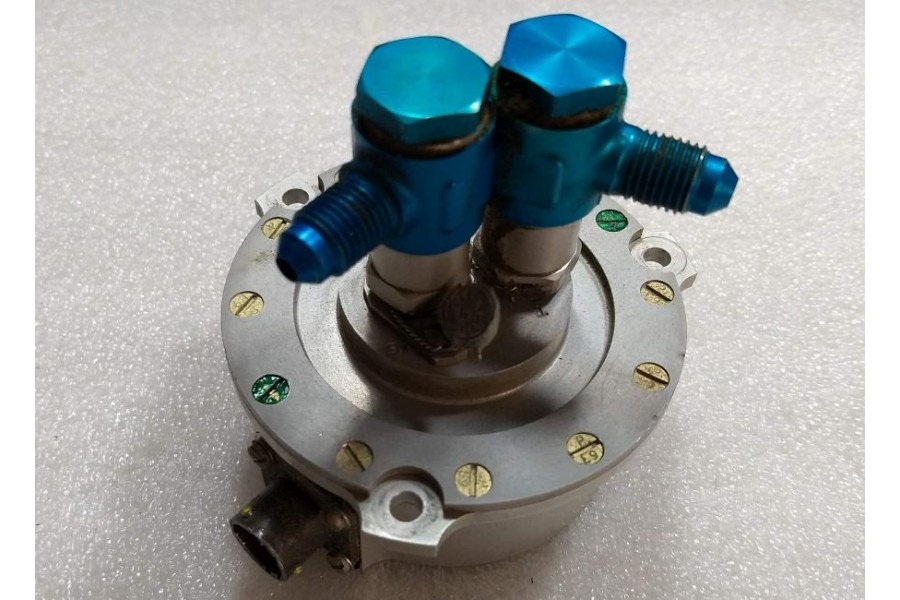
In situations where an aircraft has more than one static port, there is usually one located on each side of the fuselage. Some aircraft may have a single static port, while others may have more than one. The static port is most often a flush-mounted hole on the fuselage of an aircraft, and is located where it can access the air flow in a relatively undisturbed area. The static pressure is obtained through a static port. When airspeed increases, the ram air pressure is increased, which can be translated by the airspeed indicator. By situating the pitot tube in such a location, the ram air pressure is more accurately measured since it will be less distorted by the aircraft's structure. The pitot tube is most often located on the wing or front section of an aircraft, facing forward, where its opening is exposed to the relative wind. The pitot pressure is a measure of ram air pressure (the air pressure created by vehicle motion or the air ramming into the tube), which, under ideal conditions, is equal to stagnation pressure, also called total pressure. The pitot pressure is obtained from the pitot tube. The static pressure is used in all measurements, while the pitot pressure is used only to determine airspeed. These pressures can be measured either from the static port (static pressure) or the pitot tube (pitot pressure). It works by measuring pressures or pressure differences and using these values to assess the speed and altitude. The pitot-static system of instruments uses the principle of air pressure gradient. Several commercial airline disasters have been traced to a failure of the pitot-static system. Errors in pitot-static system readings can be extremely dangerous as the information obtained from the pitot static system, such as altitude, is potentially safety-critical. Other instruments that might be connected are air data computers, flight data recorders, altitude encoders, cabin pressurization controllers, and various airspeed switches. A pitot-static system generally consists of a pitot tube, a static port, and the pitot-static instruments. A pitot-static system is a system of pressure-sensitive instruments that is most often used in aviation to determine an aircraft's airspeed, Mach number, altitude, and altitude trend.
